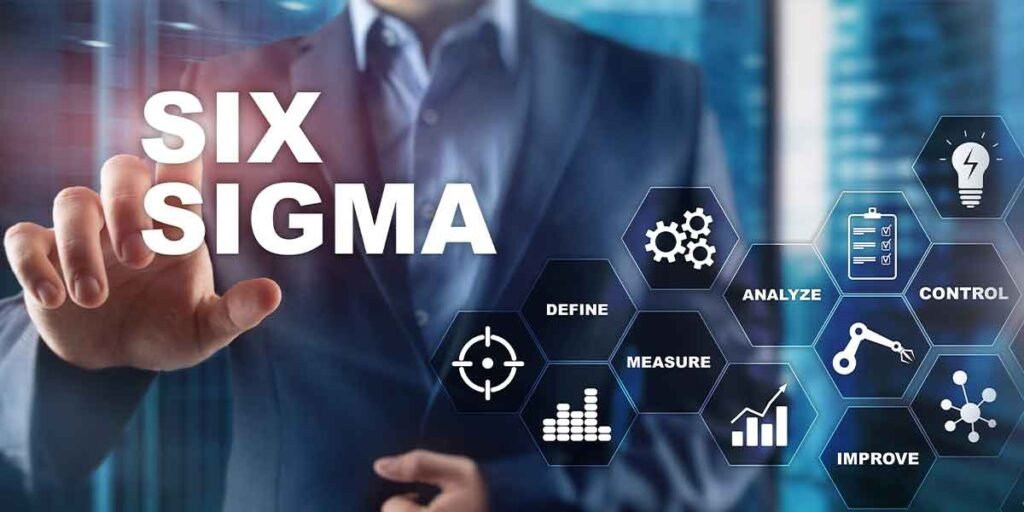
5 Phases of Lean Six Sigma
Lean Six Sigma is a process-improving method that combines the best practices of Lean and Six Sigma. In optimizing processes, Lean Six Sigma practitioners adopt the Design of Experiments (DOE), a problem-solving approach centred around 5 basic phases or stages, popularly known as DMAIC – Define, Measure, Analyze, Improve and Control.
DMAIC is ideal for improving processes, tracking progress and analyzing measurable results. The phases involved can be listed as follows:
-
Define
The first and most crucial phase of DMAIC is identifying the problems related to existing processes that need a revamp. During this phase, we define the problem by developing a problem statement and consequently, a goal statement to rectify the issue is set. Once the issue is identified, the whole process is mapped out so as to minimize or rectify the fault. The team creates a Project Charter, a high-level map detailing the process, focus, scope, goals and how it affects the stakeholders. The "Define" phase will put well-defined objectives and timelines in place for project completion.
Simply put, in this phase, we map out the process to analyze the performance and issues involved. After collecting reliable data, the Project Charter has to be updated.
-
Measure
The “Measure’ phase is meant to assess the performance of any given process. In this stage, we develop the data collection methods to measure success. The next step is to recognize input, processes and output indicators. By measuring the process, the strengths and weaknesses, including the magnitude of the problem at hand and the contributing factors can be understood and dealt with accordingly.
In simpler terms, this phase of Lean Six Sigma is meant for implementing process capability analysis.
-
Analyze
In the “Analyze” phase, the underlying causes of the issues are identified to ensure that improvement takes place from the origin of the problem so that it would be eliminated. [Lean Six Sigma certification] [Link] programs detail effective methods to identify and verify the underlying causes. Once the root cause of the problem is verified, it is updated in the project charter.
Following this phase, one will be able to chalk out all possible ways for improvement. It involves implementing process control and developing an improvement plan.
-
Improve
With the analysis done based on valid data, the next step is to improve the processes and the variables involved. In the “Improve” phase, we implement and verify the solutions through brainstorming for practical solutions. We develop maps of processes based on the implementation of different solutions and measurement of improvement like the Design of Experiments (DOE) that confirms whether the designed solutions will give the anticipated outcome.
With the analysis done and the data collected, it’s time to start making improvements. Simply put, we should determine the expected benefits of a solution and implement the same.
-
Control
Once the changes are in place, the process should be brought under control to ensure its long-term efficacy. In this phase, we maintain the solution and continually improve the process using lean principles. The main objective is to make sure that the process is managed and monitored. After the “Control phase”, you can quantify the impact of process changes in terms of efficiency, cost reduction, quality improvement, increase in productivity and customer satisfaction.
The control phase goes on continually until the need for further improvement arises. The whole DMAIC process involves time, effort and discipline which determines the improvement in processes.
Key Takeaway:
5 Stages of Six Sigma – DMAIC
- Define: Define the problem and the goals of the project.
- Measure: Measure the current process with existing data.
- Analyze: Analyze the root cause of the process.
- Improve: Improve the processes.
- Control: Control the processes for sustained results.
If you are wondering how to put DMAIC into practice to optimize processes, learn from the industry experts how to adopt the best of Lean Six Sigma to bring about organizational changes for the better.
Define
Measure
Analyze
Improve
Control
Facebook
Twitter
LinkedIn
WhatsApp
Email
Navigating the Supply Chain Certification Maze: Choosing the Right Certifying Body
Whether you are an experienced professional looking to advance your supply chain career or someone aspiring to break into the…